EURO-P3C's quality policy ensures the control of production processes, reduces anomalies and meets the requirements of our customers.
To that end, EURO-P3C deals with quality in a holistic manner, introducing complete control at each production stage, from raw material receipt to finished product delivery. We aim to involve employees to satisfy customers as well as suppliers.
A continuous Improvement approach
Our business is part of a continuous improvement process to optimise the management system, professional practices and customer satisfaction.
The success of our approach largely depends on integrating all employees through awareness and training, as well as on listening to and analysing their proposals. Human investment is paramount and thus, newly-hired people are tutored and employees continuously trained on processes and equipment.
In this context, EURO-P3C also plans process reviews and quality audits. The measurement of customer satisfaction is monitored in particular by indicators and production data. The processes' analysis and monitoring allow corrective, preventive or improvement actions if necessary.
Customer service employees are your primary contacts, and will consistently strive to meet your needs.
Finally, the Quality Management System covers all of EURO-P3C's activities to continuously improve customer satisfaction, optimise company performance and guarantee compliance with ISO 9001.
Quality certifications
Certifications by accredited bodies guarantee compliance with standards, regulations and business requirements, and are intrinsically linked to our quality approach. They represent your assurance of a compliant and high-quality product.
The ISO 9001 certification proves our daily commitment to customer satisfaction and continuous improvement.
Concerning card customisation, our sites also hold quality approvals issued by PayCert for the GIE Cartes Bancaires and by the GIE SESAM-Vitale. For the production of cheques, EURO-P3C is NF K11-112 certified and has CFONB approval.
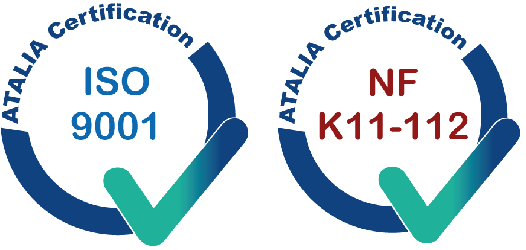
Operational EBCP
Pursuant to Regulation No. 97-02 of the CRBF, EURO-P3C has developed an EBCP, facilitated by the organisation in active-backup mode to anticipate major crises or events that could disrupt production.
The Mulhouse and Beaucouzé sites operate in mirror-backup mode: computer software and production equipment are identical, and employees have the same skills and apply identical working methods. Backup is reinforced by a multi-vendor strategy to secure supplies and ensure optimal quality.
Activities can be transferred between sites at any time and this EBCP is a working reality. Minor contingencies or production peaks regularly lead us to switch all or part of the activities between sites.
Zero-defect goal!
To achieve faultless product quality, machines are configured for continuous monitoring to eliminate any anomalies. Moreover, we conduct sampling checks at each production stage: from raw material receipt until dispatch to the customer or final carrier.
Cheques are verified for magnetic stripe quality, print quality, shaping and packaging. Likewise, we conduct consistency checks between different materials and verify thickness and weight. Regarding cards, our checks concern, for example, chip and stripe customisation, visual design printing, embedding, or the complete data consistency.
Our management tools for cheque and card production guarantee the computerised monitoring and comprehensive traceability of production and checks while maintaining a history over several years.
Finally, our operators keep machines under constant surveillance: they are indeed the ones who detect and respond to any anomalies. Their business expertise is crucial and fundamental in anticipating any process deviations early on.